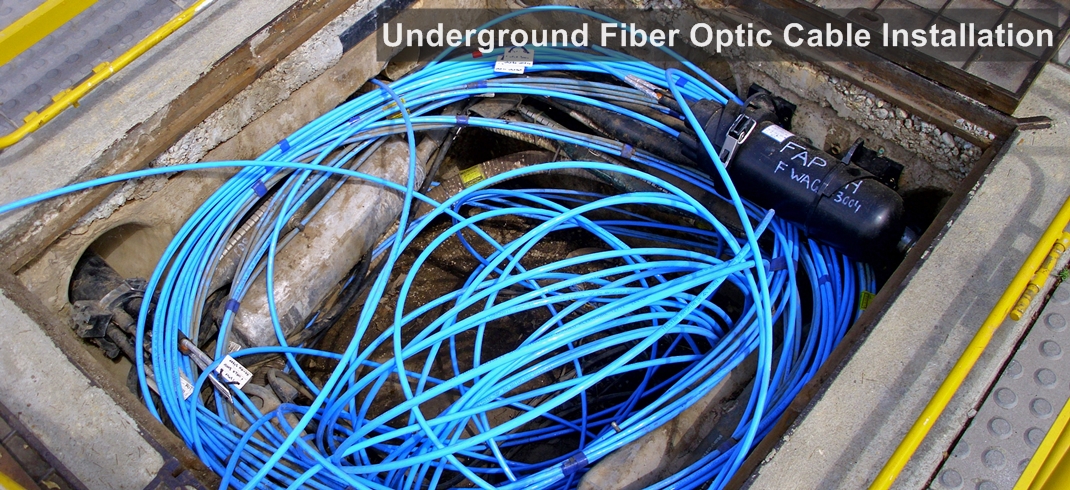
The practice of handling fiber optic cables has become much more common in recent years. Fiber optic cables are designed to withstand all typical installation and environmental stresses expected in the specific application. But it can still be damaged if not handled properly during the installation process. The two most common outdoor fiber optic cable installations are pole line aerial installation and underground cable installation. And the latter is what we are going to talk about in this tutorial.
Underground cable installation can be buried directly underground or placed into a buried duct. The cables are plowed in or buried in a trench when buried directly and the installation process can be very quick. The most common cables used for direct burial are steel armored outdoor fiber cables. While underground duct installation can protect the cables from harsh environment and provides opportunity for future expansion without the need to dig. And this is the most common practice in many areas nowadays. Another benefit is that fiber cables without armor can be used which makes the installation even easier.
Preparations and Precautions Before Underground Cable Installation
To ensure a successful job, some preparation steps are needed before the installation process.
Except for the above preparation work, all personnel must be thoroughly familiar with the following general precautions when handing fiber optic cable.
Steps for Cable Placement
Methods used for placing fiber optic cables in ducts are essentially the same as those used for placing copper cables. However, fiber optic cable is a high capacity transmission medium which can have its transmission characteristics degraded when subjected to excessive pulling force, sharp bends, and crushing forces. These losses may not be revealed until long after installation is complete. For these reasons extra care must be taken during the entire installation procedure.
Post-installation Inspection
The final thing in completing a underground cable installation is a thorough inspection of the entire route from start to finish. Engineering personnel and involved parties should inspect the construction area above ground to ensure the following:
Summary
In fact, the process of cable installation is the most aggressive event that the cable will most likely ever be exposed to, and only those specially trained people can do this job. Even for those professionals, they cannot guarantee the whole process is smooth without any problem. But adhering to the above steps and precautions can help to maximize the chance that the cable will perform properly throughout its full design lifetime.
Related Posts
-
Posted on 2020-04-22 11:06:02
Necessity of pulling grips in pulling fiber optic cables as well as the method to install the pulling grip correctly.
By Charlene -
Posted on 2020-04-08 19:18:51
Using guide and precautions about using and taking care of fiber patch cables in this post include important points such as safety attentions, fiber patch cord cleaning, and fiber cable placing.
By Howard -
Posted on 2016-04-28 18:00:07
Fiber optic cable is usually (but not always) installed in an innerduct that provides mechanical protection for the fiber optic cable. Generally, the duct is available in plastic, concrete, steel, iron and so on. As fiber optic cable is sensitive to excessive pulling, bending and crush forces, much care shall be taken to avoid cable damage during its duct installation. Methods of duct installation, installation preparation and procedures would be covered in this article. Installation Methods
By John -
Posted on 2016-04-22 17:49:00
The basics and installation methods of aerial fiber optic cables will be introduced in the article.
By Johnhttps://community.fs.com/blog/underground-fiber-optic-cable-installation.html